Location: > News
Why do aerospace materials have to use titanium alloys?
Release Date:2023-04-10
Classification:News
Titanium has an indissoluble bond with aviation. In 1953, titanium was used on the engine pod and fire wall of the DC-T machine produced by Douglas Corporation of the United States, thus unveiling the history of titanium aviation applications. Since then, titanium has been used in aviation for more than half a century. Titanium is widely used in aviation because it has many valuable properties suitable for aircraft applications. Today we will talk about why titanium alloys must be used for aerospace materials.
1. Introduction to Titanium
In 1948, DuPont of the United States used the magnesium method to produce sponge titanium in tons—this marked the beginning of the industrial production of sponge titanium, that is, titanium. Titanium alloys are widely used in various fields because of their high specific strength, good corrosion resistance, and high heat resistance.
Titanium is abundant in the earth's crust, ranking ninth, much higher than common metals such as copper, zinc, and tin. Titanium is widely found in many rocks, especially sand and clay.
Second, the characteristics of titanium
High strength: 1.3 times that of aluminum alloy, 1.6 times that of magnesium alloy, 3.5 times that of stainless steel, the highest among metal materials.
High thermal strength: the operating temperature is several hundred degrees higher than that of aluminum alloy, and it can work for a long time at a temperature of 450-500 °C.
Good corrosion resistance: acid resistance, alkali resistance, atmospheric corrosion resistance, especially strong resistance to pitting corrosion and stress corrosion.
Good low temperature performance: Titanium alloy TA7 with extremely low interstitial elements can maintain a certain degree of plasticity at -253°C.
High chemical activity: The chemical activity is very high at high temperature, and it is easy to chemically react with gas impurities such as hydrogen and oxygen in the air to form a hardened layer.
Small thermal conductivity and small elastic modulus: thermal conductivity is about 1/4 of nickel, 1/5 of iron, and 1/14 of aluminum, and the thermal conductivity of various titanium alloys is about 50% lower than that of titanium. The elastic modulus of titanium alloy is about 1/2 of that of steel.
3. Classification and application of titanium alloy
Titanium alloys can be divided into heat-resistant alloys, high-strength alloys, corrosion-resistant alloys (titanium-molybdenum, titanium-palladium alloys, etc.), low-temperature alloys, and special functional alloys (titanium-iron hydrogen storage materials and titanium-nickel memory alloys) according to their uses. wait.
Although the history of the application of titanium and its alloys is not long, it has won many honorary titles because of its superior performance. The first title won was "Space Metal". It is light in weight, high in strength and high temperature resistant, and is especially suitable for manufacturing aircraft and various spacecraft. At present, about three-quarters of the titanium and titanium alloys produced in the world are used in the aerospace industry. Many parts that were originally made of aluminum alloy have been replaced with titanium alloy.
4. Aviation application of titanium alloy
Titanium alloys are mainly used for aircraft and engine manufacturing materials, such as forged titanium fans, compressor discs and blades, engine covers, exhaust devices and other parts, as well as structural frame parts such as aircraft beams and frames. The spacecraft mainly uses the high specific strength, corrosion resistance and low temperature resistance of titanium alloys to manufacture various pressure vessels, fuel storage tanks, fasteners, instrument straps, frames and rocket shells. Artificial earth satellites, lunar modules, manned spacecraft and space shuttles also use titanium alloy plate weldments.
In 1950, the United States used it on the F-84 fighter-bomber as non-load-bearing components such as rear fuselage heat shields, wind deflectors, and tail covers. Since the 1960s, the use of titanium alloys has moved from the rear fuselage to the middle fuselage, partially replacing structural steel to manufacture important load-bearing components such as bulkheads, beams, and flap slide rails. Since the 1970s, a large number of titanium alloys have been used in civilian aircraft. For example, the amount of titanium used in Boeing 747 passenger aircraft is more than 3640 kg, accounting for 28% of the weight of the aircraft. With the development of processing technology, a large number of titanium alloys are also used in rockets, artificial satellites and spacecraft.
The bigger the plane, the more titanium it uses. The titanium alloy used by the American F-14A fighter jet accounts for about 25% of the machine weight; the F-15A fighter jet accounts for 25.8%; Aircraft with high titanium content.
5. Reasons why titanium alloys are widely used in aviation
The flight speed of modern aircraft has reached more than 2.7 times the speed of sound. Such a fast supersonic flight will cause the aircraft to rub against the air and generate a lot of heat. When the flight speed reaches 2.2 times the speed of sound, the aluminum alloy can't stand it. High temperature resistant titanium alloy must be used.
When the thrust-to-weight ratio of the aero-engine increases from 4 to 6 to 8 to 10, and the outlet temperature of the compressor increases from 200 to 300°C to 500 to 600°C, the original low-pressure compressor discs and blades made of aluminum must be replaced with titanium alloy.
In recent years, scientists have continuously made new progress in the research work on the properties of titanium alloys. The original titanium alloy composed of titanium, aluminum, and vanadium has a maximum working temperature of 550°C to 600°C, while the newly developed titanium aluminum (TiAl) alloy has a maximum working temperature of 1040°C.
Using titanium alloy instead of stainless steel to manufacture high-pressure compressor discs and blades can reduce the weight of the structure. For every 10% reduction in weight of an aircraft, 4% of fuel can be saved. For the rocket, every 1kg of weight reduction can increase the range of 15km.
6. Analysis of machining characteristics of titanium alloy
First of all, the thermal conductivity of titanium alloy is low, only 1/4 of steel, 1/13 of aluminum, and 1/25 of copper. Due to the slow heat dissipation in the cutting area, it is not conducive to thermal balance. During the cutting process, the heat dissipation and cooling effects are very poor, and it is easy to form high temperature in the cutting area. Reduced durability.
Secondly, the thermal conductivity of titanium alloy is low, so that the cutting heat is accumulated in a small area near the cutting tool and is not easy to dissipate. The friction force of the rake face increases, it is not easy to remove chips, the cutting heat is not easy to dissipate, and the tool wear is accelerated. Finally, the chemical activity of titanium alloy is high, and it is easy to react with the tool material when processed at high temperature, forming dissolution and diffusion, resulting in sticking, burning, and breaking of the knife.
Have questions,
Welcome to call anytime!
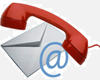
We provide you with materials and design solutions based on your needs.
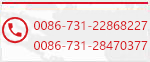